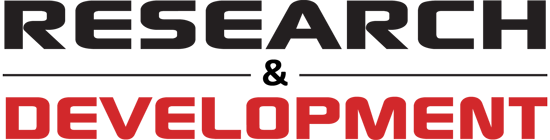
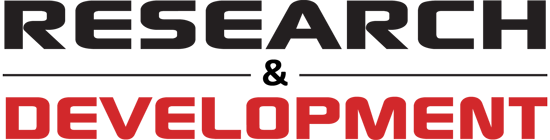
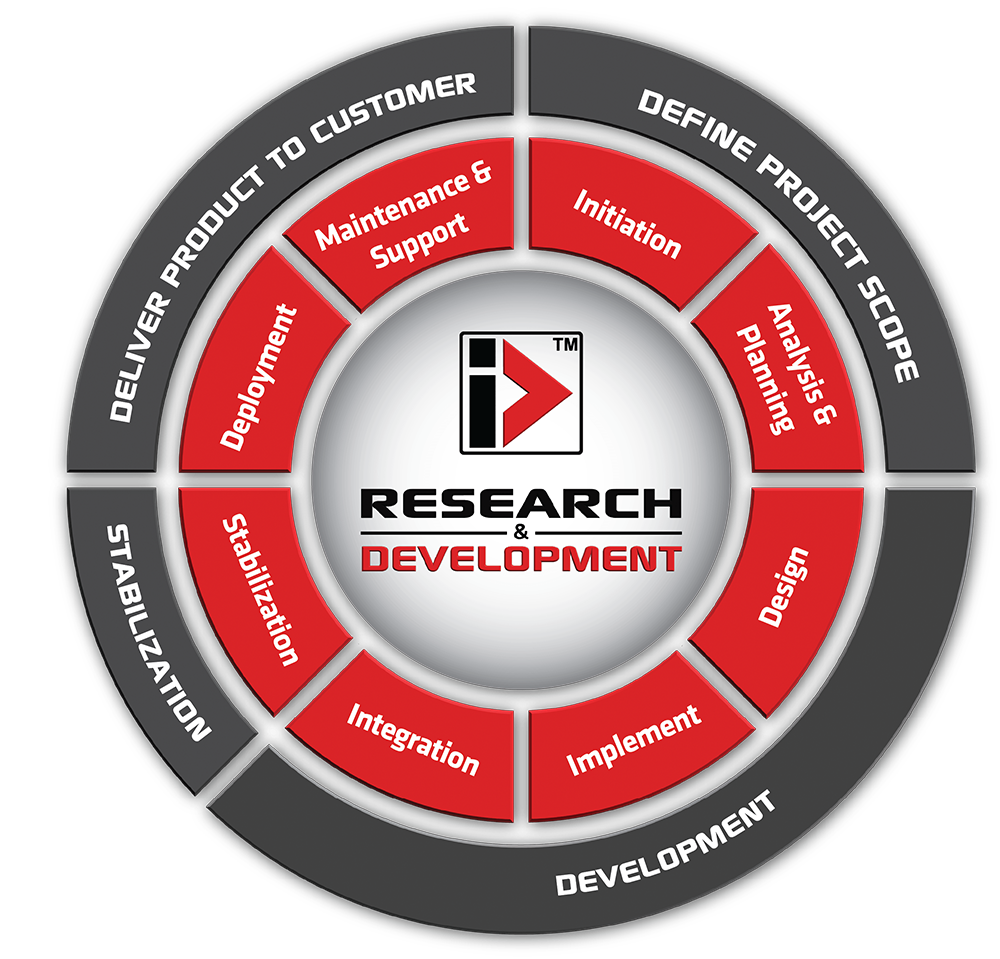
The Makuri group is constantly innovating through the testing and using new designs and materials that will deliver ever-increasing value to mining customers.
To our knowledge, few, if any, other mining wear-systems companies spend the amount of time or money in ratio to sales on Research and Development as we do.
We have specifically developed our materials and composites. They are proven to deliver the lowest TCO in their area of use, and many are also covered under patent protection.
Laboratory Testing
In House
External Independent
We use a variety of 3rd party testing laboratories for both R&D and quality control purposes. These include, but are not limited to;
- The University of Newcastle Research Association (TUNRA) and their Bulk Materials Testing facilities for all field simulated abrasive and impact wear benchmarking.
- INTERTEK laboratories and inspection services globally for destructive testing and Quality Assurance and certification to meet international standards such as ISO9001.
Current Projects
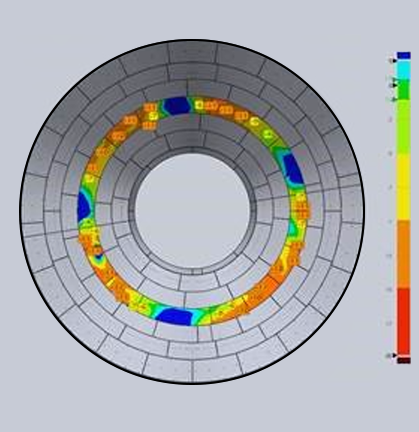
Advanced Wear Monitoring Systems
Viewcurrent projects
Advanced Wear Monitoring Systems
Makuri Technology has completed a development agreement with Qalasadi of Singapore, a renowned high-end technology developer, to jointly develop a new range of wear monitoring technologies, especially for mining applications. This allows Makuri to move ahead of the current range of offerings that lack application diversity and are unreliable over more extended periods. Mining and industry, in general, need such better technologies, and we shall deliver them. Qalasadi principal Mr Khurram Hamid has a Master’s Degree in Engineering, Industrial Automation, and Robotic Engineering and will also join the executive team of Makuri. Khurram has over 20 years of outstanding performance in product design & development and is a serial inventor and multiple patent developer. His work in mining has covered smart pigging and various wear monitoring technologies. He is the R&D advisor and technology developer for all Makuri projects that fall within his areas of expertise.
We expect the first system designed for reclaim feeders to be installed by late 2022.
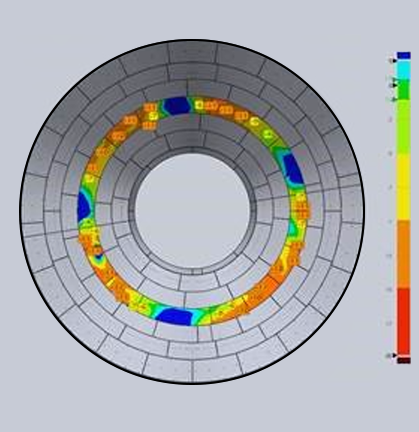
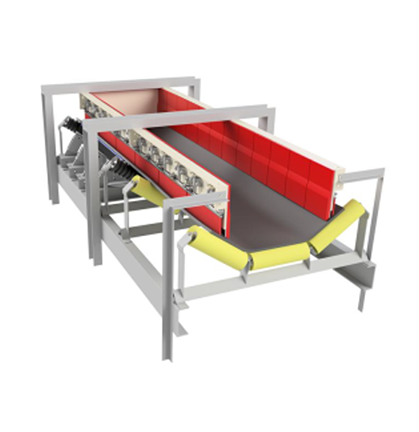
Zero Manual Handling Conveyor Skirting Liner Systems
Viewcurrent projects
Zero Manual Handling Conveyor Skirting Liner Systems
There are huge issues surrounding the safe work practices of installing and removing internal conveyor skirting liners, the associated environmental impact of poor design and maintenance and the overall high cost of operating such systems. These issues cover confined space, manual handling weight limits, material spillages and production losses.
We are in the progress of developing many designs that address some or all of these issues, and some are in field trialling. We expect to release a full range of products in this area in 2023.
There are few suppliers who specialise in the design and supply of high-performance internal skirting liners
- Integrated Internal & External
- Robotic Zero Manual handling
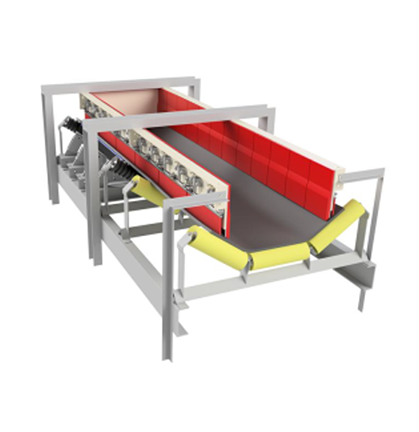
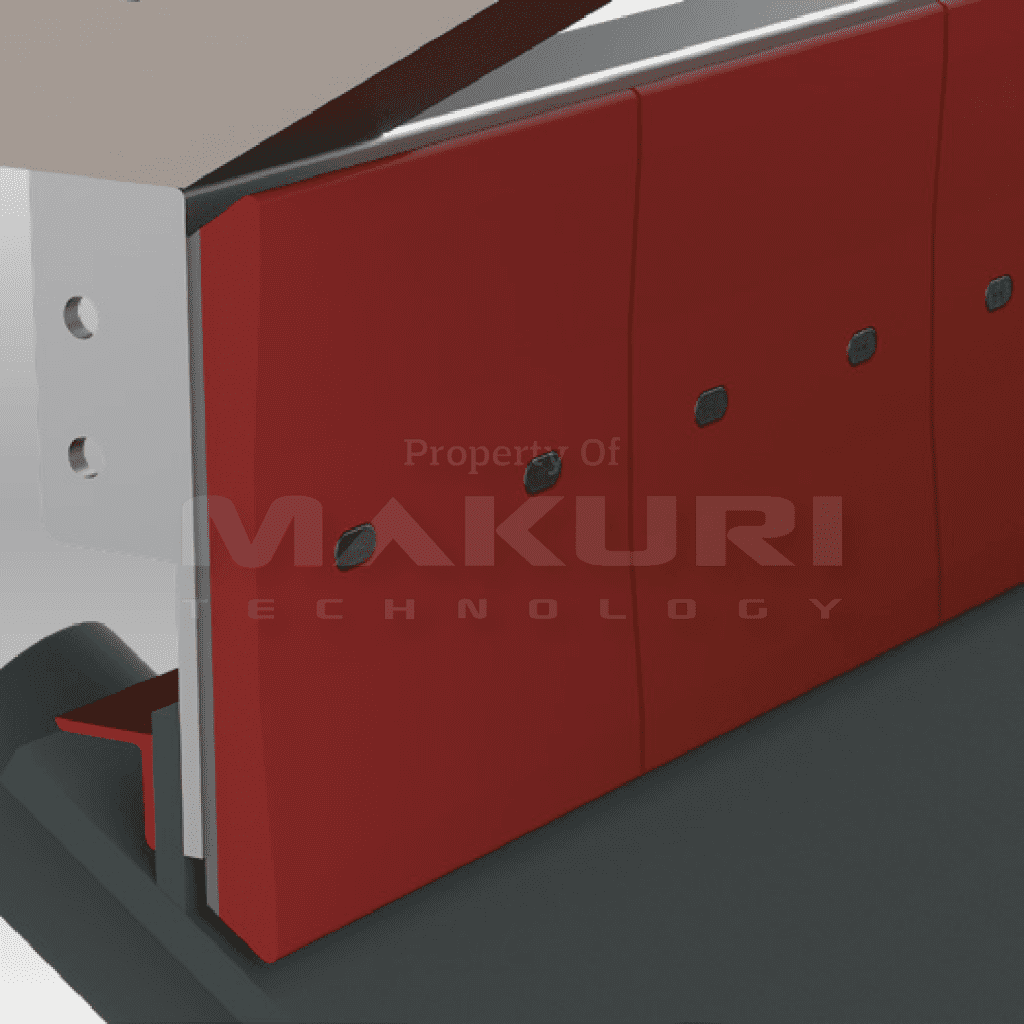
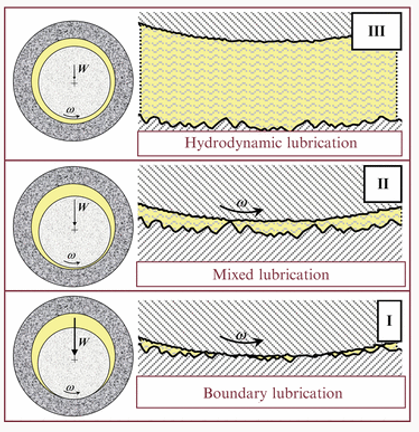
Crusher Lubrication
Viewcurrent projects
Crusher Lubrication
The designs of gyratory crushers and larger cone crushers prevents correct full film lubrication on major bearing surfaces. This leads to rapid bush wear and failure, high power draw, high costs and downtime. There is a need for advanced, made-for-purpose crusher lubricants that address all of these issues. We will move to field trialling and testing after finishing all laboratory tests.
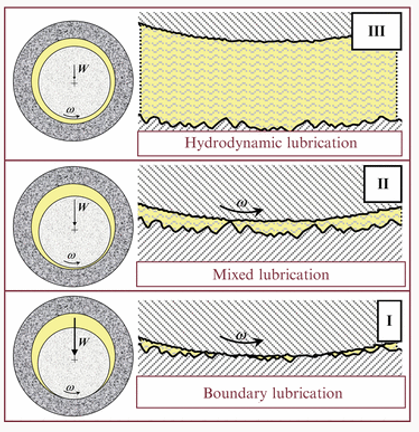
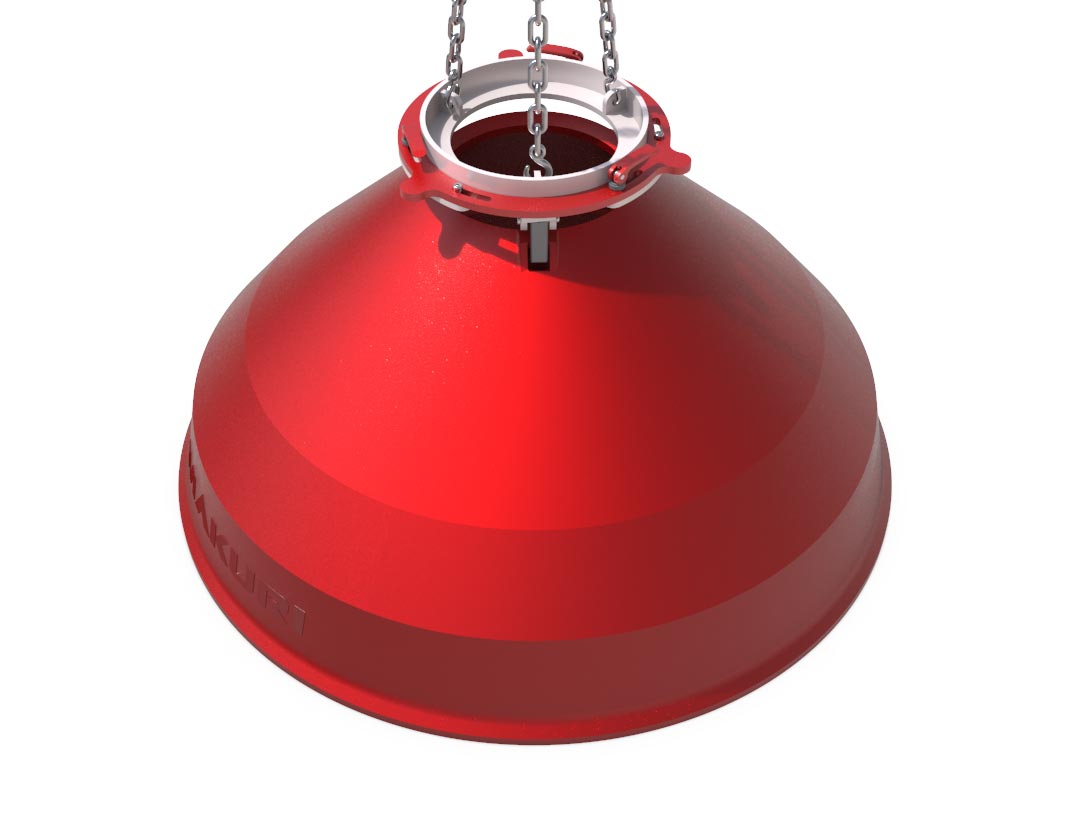
Installation & Safety Devices
Viewcurrent projects
Installation & Safety Devices
Makuri Technology has developed a selected range of proprietary and patented safe lifting devices covering jaw and cone crushers and chute liners
- Jaws
- Cones
- Chutes
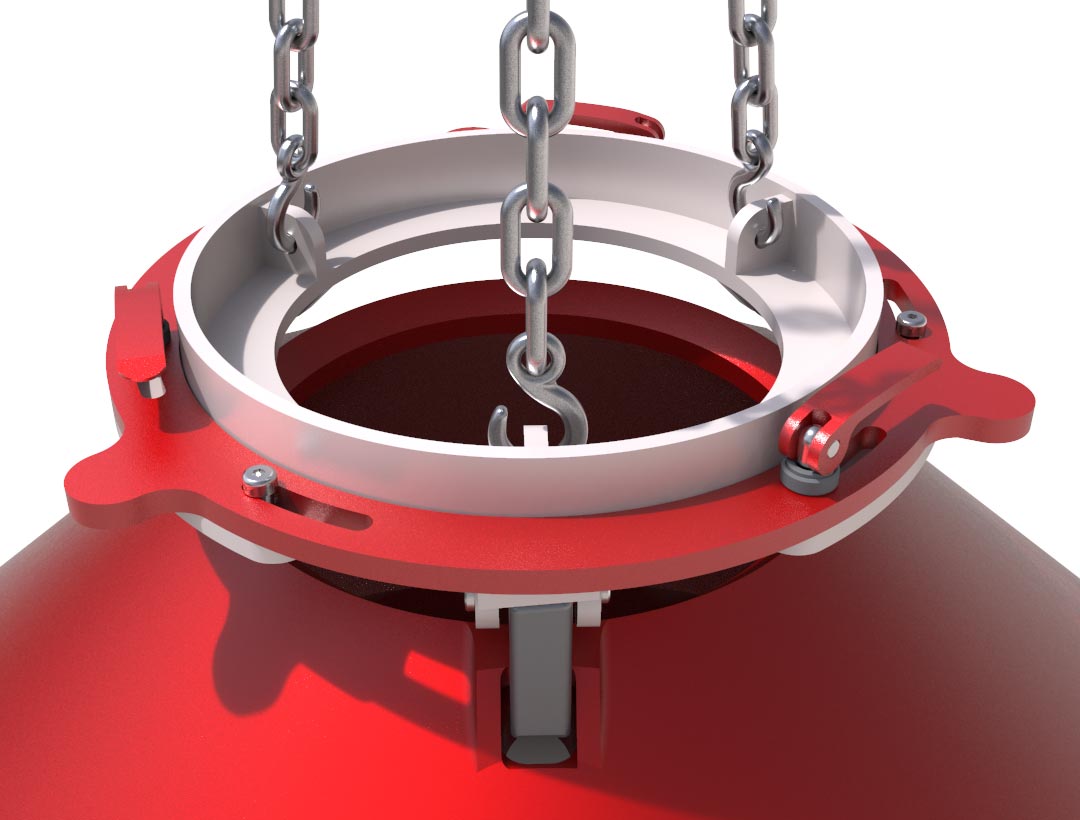